Medical Device Rubber and Plastics Component Manufacturing & Assembly
Bring medical device innovations to life. Faster.
Minnesota Rubber & Plastics helps medical device manufacturers unlock the full potential of materials science to bring highly valuable and differentiated products to market. With direct access to the industry’s foremost materials science, fully functional prototyping, and our manufacturing experts, we are ready to engage with you and your team now. If you’re looking for fresh, new ideas for rubber, silicone, or thermoplastic components, it’s time to engage us.
Our new Innovation Center is now open! This exciting addition allows our customers to innovate and bring their products to market faster.
For more details, watch the video!
Innovation Capabilities Overview
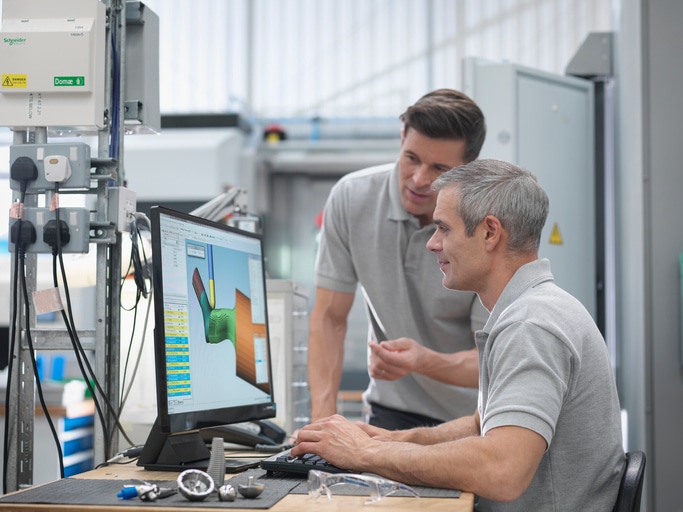
End-to-end medical device capabilities
Materials development, fully functional prototyping, custom component design & manufacturing.
We work with medical device companies to produce critical-to-function components. We offer deep expertise in custom rubber formulations, silicone (including LSR), thermoplastics and component assemblies built for high performance and reliability. Our ISO-13485-certified global manufacturing facilities offer Class 7 and 8 clean room capabilities.
Examples of our Services Include:
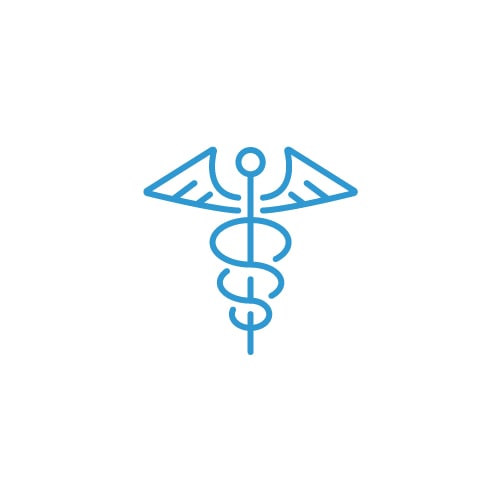
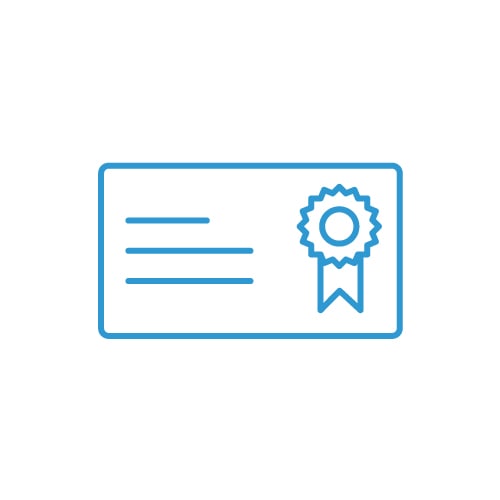
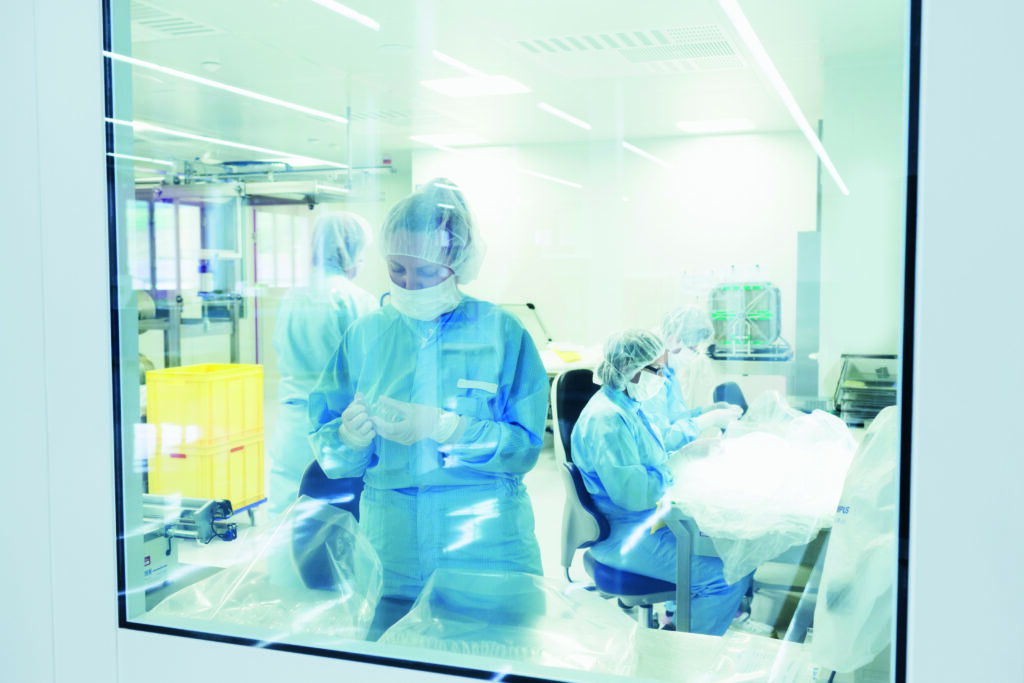
Now Part of Trelleborg
Trelleborg Healthcare & Medical is one of the world’s leading developers, manufacturers and suppliers of precision seals, bearings, and custom-molded polymer components for demanding medical device, biotech, and pharmaceutical applications. With our global footprint, we help customers innovate their medical device, biotech, and pharmaceutical applications, including:
- Biopharmaceutical
- Cardiovascular
- Cell Therapy
- Diabetes
- Diagnostics
- Sterile Fluid Connectors
- Structural Heart
- Surgical Instruments
- Targeted Drug Delivery