Rubber and Plastics Product Design, Testing & Development
Let us be Your Rubber and Plastics Design Experts
For companies looking to partner with us, we utilize a seven stage NPD process that allows for a collaborative process ensuring ultimate success in delivering a customized solution that exactly meets your needs.
Underpinning NPD is our adherence to disciplined processes in materials development, product design, tooling development and quality control ensuring a robust, rapid and safe launch of all products.
Our 7 stage processes includes the following gates
1. Opportunity Assessment
2. Specification Gathering
3. Product Development and Analysis
4. Prototype Development (simulations and modeling)
5. Production development
6. Process design and development (scientific molding optimization)
7. Production control
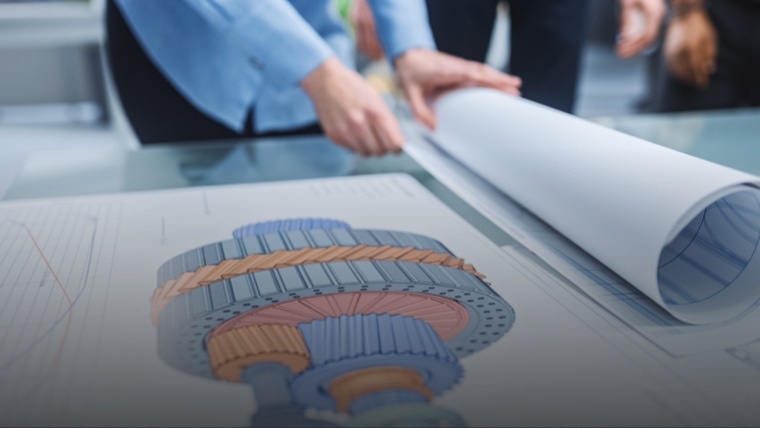
Product Design
Seal design can be very complex and is often the most important component in a product. Seals must be carefully designed and produced to ensure optimal performance in their application.
All sealing applications fall into one of three groups:
- Static – Applications where there is no movement
- Reciprocating – Applications where there is linear motion
- Rotary – Applications in which there is high speed rotation
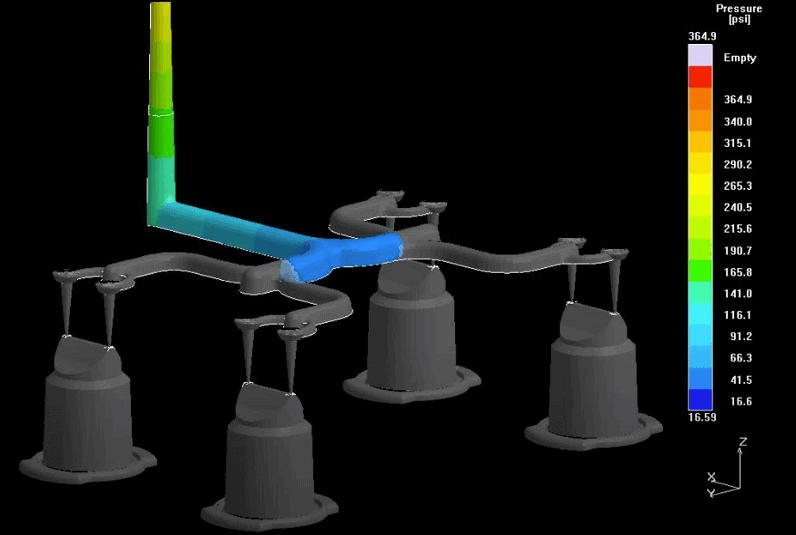
Mold Flow
Mold flow analysis, or MFA, is a method for modeling the behavior of material in the mold during the molding process. It allows us to predict how the material will flow and cure during the molding process that will ultimately govern the final geometry of the molded part.
We utilize state of the art advanced analytic software optimized for both Elastomers and Thermoplastics to ensure a robust manufacturing process is designed prior to any product launch.
MFA modeling allows us to predict:
- 3D flow effects
- Temperatures and pressures within the mold
- Defects such as flow lines and air trap
- State of cure
- Cycle Times
- Thermally induced residual stresses and distortion for die and inserts
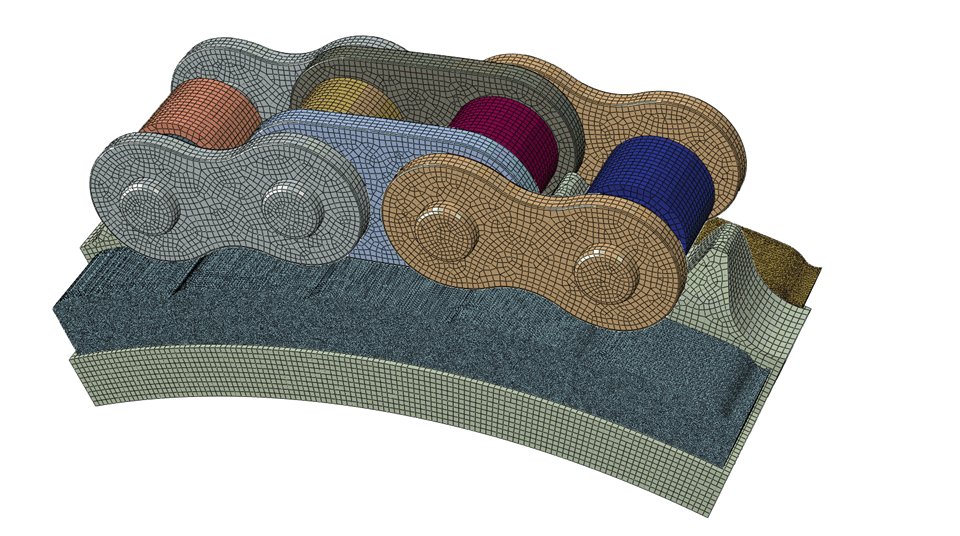
Finite Element Analysis (FEA)
FEA, is a method to model part performance under operational constraints. FEA can predict Stress, Strain, Displacement, and Contact Pressure in any application environment.
Material properties are characterized and boundary conditions are entered to give you the most accurate simulation of how a part or assembly behaves in the real world. Results are reviewed by a highly experienced team of Design Engineers and recommendations are provided. FEA can reduce time to market and Customer development costs via robust simulation methods.

Prototyping
Through our rapid prototyping plan, we can quickly fabricate a scale model of a part or assembly.
These models can be used for testing and to create models for tooling, such as with silicone rubber molds. Furthermore, our prototyping strategy is to ensure that any part developed is scalable to a production environment thus ensuring predictability and repeatability in material, design and manufacturing process.
The benefits of rapid prototyping include:
- Decreased development time
- Elimination of design errors
- Minimized engineering changes
- Decreased product launch timeframe
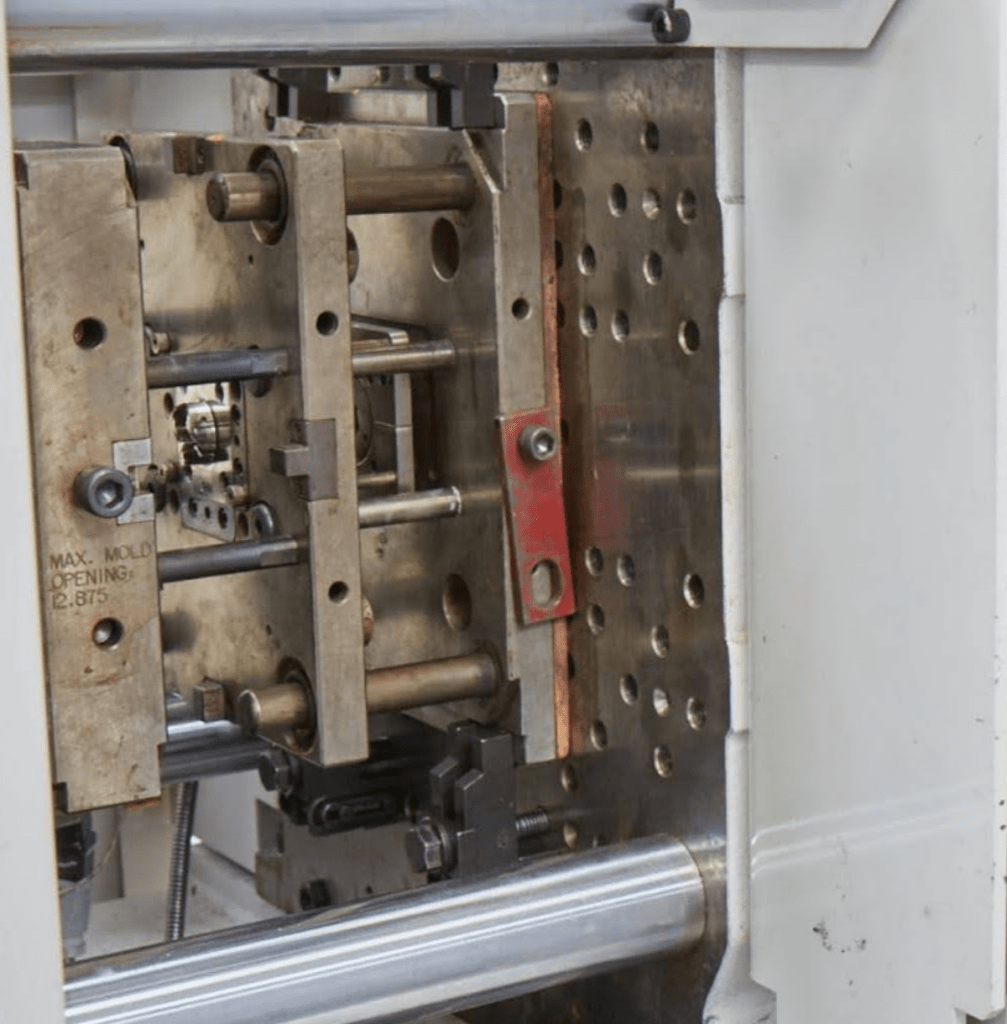
Tool Design & Build
The recommended mold configuration and molding process depend upon the size and complexity of the part, the anticipated production volumes, types of materials and part functionality.
MRP supervises all aspects of the design and tool fabrication process through a dedicated team of highly experienced tooling engineers. We have an extensive range of capability to support all of our manufacturing options for rubber, silicone, LSR, and thermoplastic including compression, transfer, insert over molding, and injection molding. We make every effort to match the tooling concept to the anticipated volume, part and application requirements.
Quality
Underpinning our product launch process is our strict adherence to quality protocols & systems that are designed to ensure compliance with the most rigorous standards used in the Medical industry.
New programs have extensive IQ, OQ and PQ protocols completed where the product process is challenged and parts are run at extreme process inputs to ensure all specifications are met within the defined process window. This culminates in completed validation and PPAP.